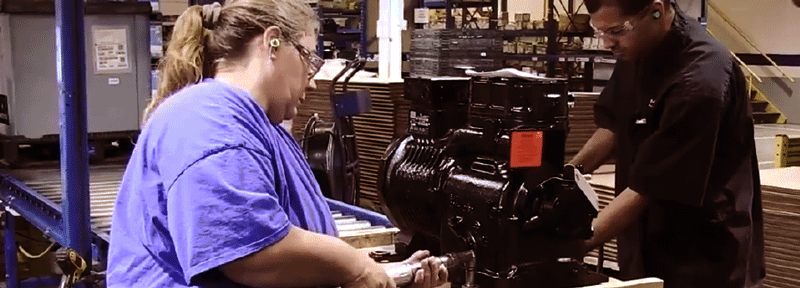
Many contractors use the word rebuilt and remanufactured interchangeably. However, there is a significant difference between the two. A rebuilt compressor addresses the visible problem and is only replaced with parts that are either worn out or no longer usable. Even if there is a part that might potentially stop working in the near future, causing a problem to the compressor, it will not be replaced until it is completely unusable. On the other hand, a remanufactured compressor is remanufactured to the latest OEM Spec. It addresses not only the visible problems but also the underlying complications. All the parts including ones that are still functioning or outdated are replaced to meet the latest manufacturing specs of a brand-new compressor. Remanufactured compressors go through an extensive process of being disassembled, cleaned, gauged, and tested to verify all parts are up-to-date and meet UL certification.
Here are the top 3 reasons to choose a remanufactured compressor over a rebuilt/reworked compressor.
- Peace of Mind
A rebuilt compressor may have a combination of new, used, and worn-out parts. If there are some parts that are worn out but still meet the rebuilder’s normal wear standard, it will not be replaced. Many rebuilders use a single gasket thickness regardless of the specification for optimal performance. On the other hand, with a remanufactured compressor, you are guaranteed to receive a compressor that meets the latest standard of a brand-new compressor. It has been torn down to identify any problems and fix issues that are not visible. All parts are thoroughly inspected and gauged for wear and tear and are replaced. In addition, parts such as valve plate gaskets are selected based on the deck height of the cylinder pistons, further providing reliability and improved performance. All Copeland certified remanufactured compressors are UL certified and backed by the same warranty as the new models. More than 500 parts are either replaced or upgraded!
- Reputation
As a contractor, your personal and company reputation is the key to improving your image and building upon recurring business. Homeowners and customers look to you as the experts in the industry and want to be assured you will take care of all their HVAC needs with the right OEM certified parts. The ability to give your customers a peace of mind by insuring them that their problems would be fixed, will help your reputation significantly. To achieve this, as a contractor it is important to use a Copeland certified remanufactured compressor. Remanufactured compressors provide reliability, optimal performance, and safety. It also prevents future system failures, costly customer call backs and installations hassles.
- Thorough Process
With a remanufactured compressor, all parts that are worn out or do not function are replaced down to the core, making it essentially a brand new compressor. As an example, here is the process that all Copeland Certified semi-hermetic compressors go through.
- Teardown – When compressors are received in the Copeland facility from buy backs and salvage programs, they are completely disassembled in ordered to be replaced and upgraded with newer parts. This includes oil check valves, name plates, oil pickup tubes, piston rod assemblies, seals, and bearings.
- Cleaning – After the disassembly, all parts are thoroughly cleaned to remove any chemical residue.
- Qualification – In order to prevent any future problems, all worn out parts are inspected and requalified before reusing or replacing the part. Parts that do not meet the latest engineering requirements are replaced with new or requalified parts.
- Assembly – All components are identified and verified before they are put into the remanufactured compressor. In each assembly station, the part that would go into a remanufactured compressor is highlighted so the technician can easily identify the required components, mitigating the risk of placing the wrong piece into the compressor. If an incorrect part is chosen, the assembly will come to a stop and prevent the technician from continuing the process.
- Repainted – Compressors are then sent to an auto paint station to provide consistent color coverage and prevent them from rusting.
- Inspection – By the end of the process, compressors are thoroughly inspected for electrical and mechanical performance verification. Both brand-new and remanufactured compressors are packaged in the same line and shipped to the OEMs!
How has your experience been with a rebuilt or a remanufactured compressor? Let us know your feedback below!